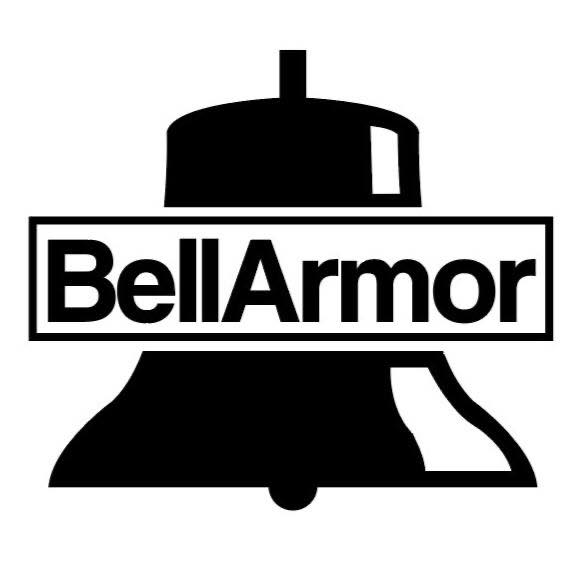
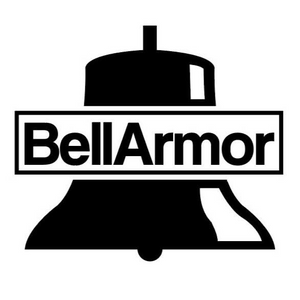
About Parkerizing
Parkerizing or Phosphating is a metal finish that really gained in popularity during WW2 when the US Government was looking to replace the typical blued finish on most small arms with a Rust Resistant and Anti Reflective coating that would be both Durable and Abrasion Resistant and hold up in all weather extremes, for this they chose Parkerizing or Phosphating.
The Parkerizing technique is a Phosphate etching process that produces a hard Matte or Dull finish that is actually etched into the surface of the metal, it is both very Durable and Anti Reflective and with excellent oil holding properties.
The most commonly types used are the original WW2 type, known as Grey or Zinc Oxide and the latter Black Manganese, still in use by many Military and Civilian Manufacturers in many countries on a wide variety of products.
The standard Grey Oxide may range from light grey to a darker grey depending on the type and hardness of the metal it is being applied to, whereas the Black Manganese will usually always be in the Charcoal Black category.
Either type of Parkerizing Finishes will offer much more protection from harsh weather than bluing with Black Manganese offering the highest level. Both types are very simple to apply and maintain.
Parkerizing is much easier to use than bluing because as it is a Matte Finish the parts or items you want to Parkerize do not have to be polished, they can be acid dipped, sanded, bead blasted or sand blasted. In fact a lot nicks and scratches that would show up on a blued item would not even be seen after Parkerizing.
Parkerizing is an immersion process requiring the solution to be heated to approximately 170-185 degrees and the dipping time can range from 5-45 Minutes or so, depending on the hardness of the metal and the desired thickness of the coating.
It can be used on any type of Mild or Gun steel, it is not for use on Stainless or any types of Aluminum.

About Us